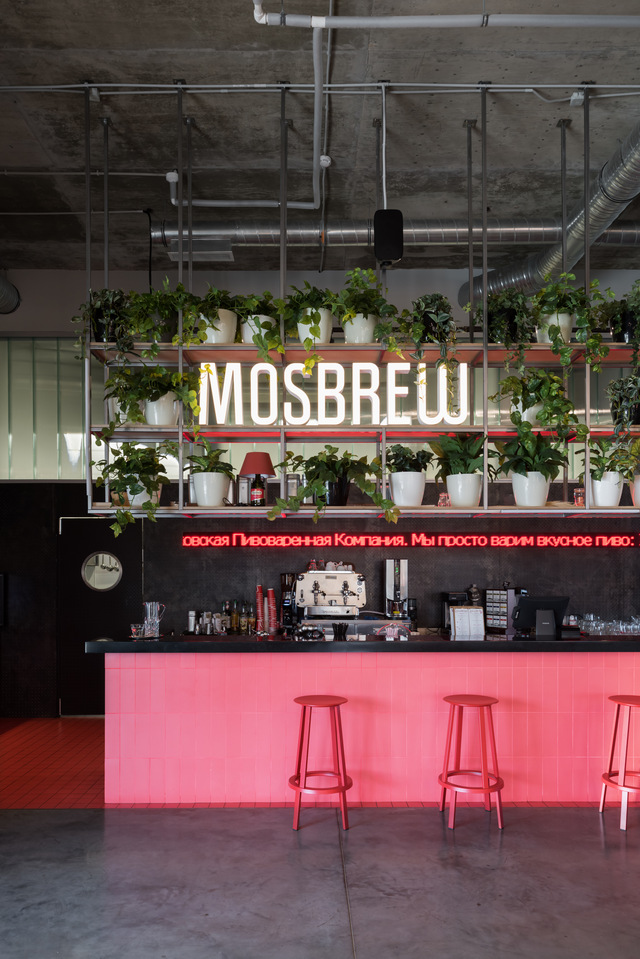
Работа любого производства начинается с хорошо организованного склада. Нет поставок сырья — останавливаются все процессы. Менеджер центрального материального склада Алексей Волчков рассказывает, как компания увеличила производительность, в чём плюсы узкопроходной технологии и сколько проезжает погрузочная машина за свой «жизненный цикл».
Главная сложность
Есть два подразделения: центральный материальный склад (ЦМС) и склад готовой продукции (СГП). Они должны функционировать постоянно. ЦМС, как рота боевого обеспечения, должен беспрерывно поставлять «припасы» для производства. Компания ведь не может остановить работу ради переустройства складов. Поэтому мы решили поделить всё пространство на четыре сегмента — «захватки», — которые поочередно обновляем без ущерба другим процессам Московской Пивоваренной Компании. Сейчас полностью реализованы три зоны, в четвёртой шлифуют полы, там скоро начнём монтаж стеллажей.
Менять нужно даже пол
Одна из главных задач модернизации складов — увеличение вместимости. Для этого мы решили применить узкопроходную технологию. Так стеллажи стоят плотнее, и пространство используется рациональнее. Требования к полу, соответственно, поменялись, ведь шесть-семь ярусов товара давят на него сильнее, чем один. Каков план действий? Сначала нужно укрепить грунт: на расстоянии двух метров друг от друга делают отверстия, в которые заливают специальный раствор, чтобы фундамент был прочнее. На втором этапе сотрудники компании Klindex шлифуют покрытие. В прошлый раз мы делали иначе: укладывали на пол выравнивающий полимерный состав. В текущем проекте решили попробовать другую технологию. В Klindex почти не используют химию, сразу выравнивают всё итальянскими машинами с 14 уровнями шлифовки. После них бетонный пол становится идеально ровным, фактически зеркальным. Это необходимо, чтобы узкопроходный штабелёр мог без лишних колыханий проехать между стеллажами.
Безопасная работа
Были случаи, когда штабелёр подъезжал с одной стороны стеллажа, брал палету с какого-нибудь яруса и случайно сталкивал соседнюю — та падала и разбивалась. Такое недопустимо. Сейчас между стеллажами вообще нет людей — только узкопроходные машины. По большей части они автоматические: получают сигналы от ВМС-системы, подъезжают, сканируют нужный адрес и штрихкод с груза. Передвижение обеспечивает индукция — канал в полу, куда заложены провод и транспондеры, к которым привязываем машину.
Кроме того, мы перестраховываемся и несколько раз проверяем на прочность новые стеллажи. Производитель, у которого их покупали, даёт гарантии качества и безопасности, но мы приглашаем для дополнительной проверки независимую компанию — нашего многолетнего партнёра. Специалисты составляют подробный отчёт, и, опираясь на результаты, мы решаем, готовы к работе участки или нет.
Эффективность и качество хранения продуктов
Раньше комплектовщик забирал груз вручную. Это, как уже выяснили, опасно и неэффективно. Прежде такая система была приемлема, но мы ставим перед собой новые цели, и теперь низкая производительность труда нам не подходит. Собираемся внедрить гравитационный коробочный стеллаж — в нём есть каналы, в которые загружается SKU (идентификатор товарной позиции, артикул). Комплектовщику не придётся прилагать много усилий, чтобы достать груз: он будет опускаться автоматически под собственным весом. Также изменится технология сборки. Раньше мы брали заказ, его комплектовал один человек, загружал пустую палету — например, пять коробок пива «Жигули Барное», столько же «Хамовников». Сейчас мы берём 10 заказов и раскладываем по 10 пустым палетам: один человек положит пять коробок с «Жигулями», а второй — три с «Хамовниками». Это должно увеличить производительность труда.
Так мы постепенно избавимся и от напольного хранения на всех складах. Оно неудобно тем, что нет доступа к отдельным грузам и под своим весом палеты деформируются, — из-за этого страдает качество. В стеллажах прописываем топологию и соблюдаем товарное соседство. Например, химию мы не будем держать ни с чем другим. Солоды, которые могут заразить аллергенами другое сырьё, тоже хранятся отдельно.
Универсальность помещений
ЦМС своими грузами и бизнес-процессами отличается от СГП. Для первого важно не останавливать производство, а для второго — удовлетворить клиента и ретейлера. В СГП все грузы более или менее стандартизированы: высота до 1,6 метра, вес не больше 800 килограммов. В ЦМС же они всевозможных форматов: складные гиттербоксы, палеты с сахаром (общий объём хранения — более 60 тонн), грузы со свесом.
Сейчас склад стал универсальным, его можно использовать для двух подразделений. Вот гипотетическая ситуация для примера. Балки в стеллажах установлены под стандарт готовой продукции СГП. Мы решаем, что он переезжает в построенный через дорогу «Хрустальный остров» — на новый склад. ЦМС остаётся на месте. За час перебиваем балки на другую высоту и сразу начинаем работать с его грузами. Ещё один пример: СГП остаётся, но теперь нужно дополнительное место для сырья и материалов, — принимаем решение арендовать склад. Материалы переезжают, опять перебиваем балки, и всё готово.
Какие компании с нами сотрудничают
План модернизации склада мы начинали прорабатывать ещё в 2018 году, более детально и подробно взялись в июне 2019-го. Нам предлагали услуги крупные логистические партнёры: Toyota, Jung, Linde, Stihl.
На старом складе нас обслуживает Jungheinrich, а на новом — Linde. У машин второй компании лучше эргономические характеристики, есть стабилизация устойчивости груза (находясь на высоте, он не раскачивается и остаётся статичным). Работают они на литийионных батареях. Им не нужны специальные зарядные устройства и помещения, в отличие от свинцовых. Всё просто, почти как с батарейкой в телефоне.
НЕМНОГО ЦИФР
На ЦМС работают 70 человек, на СГП — 170.
Склад работает 7 дней в неделю, 24 часа в сутки, 363 дня в году. 1 и 2 января — выходные.
Вместимость склада увеличилась почти в два раза. Раньше здесь хранили около 10–13 тысяч палет, а сейчас — 20–23 тысячи.
Если собрать все банки со склада вместе, получится башня высотой 16 700 километров — 30 925 Останкинских башен.
Одна из погрузочных машин за свою «жизнь» проехала 2 520 000 километров — три рейса до Луны и обратно.
Мы используем cookie и другие похожие технологии для улучшения работы сайта