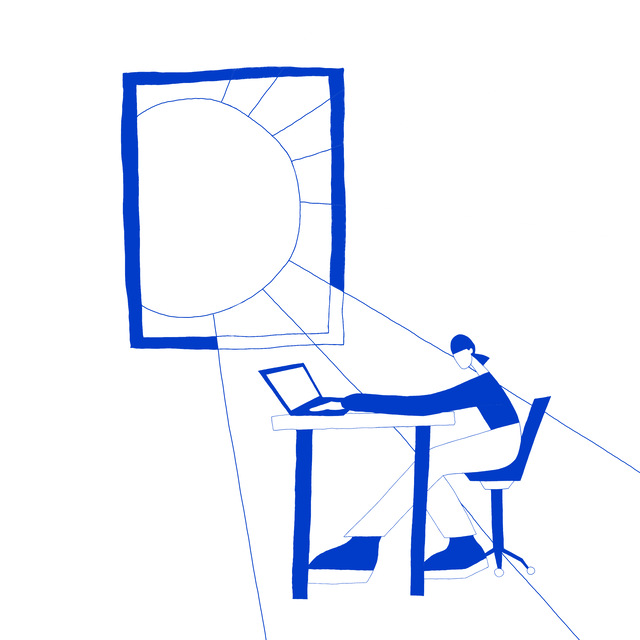
Наш завод входит в десятку самых энергоэффективных пивоварен в мире. Из года в год мы инвестируем в технологии, позволяющие сохранять ресурсы как природные, так и финансовые. Мы поговорили с менеджерами по эффективности Алексеем Поляковым и Константином Коротаевым о том, зачем был запущен проект «Энергоэффективность» и почему он важен для завода.
Мы много инвестируем в энергоэффективные технологии. Как это помогает при производстве и почему это так важно?
Константин Коротаев: Мы сейчас проверяем все процессы на внутренние ресурсы для ещё лучшей экономии. Ищем какие-то неполадки. С запуска завода прошло уже 10 лет, за такое время оборудование изнашивается. Например, где-то удельное потребление могло увеличиться. Сейчас идёт проверка, систематизация и подготовка плана по более эффективному использованию ресурсов.
Алексей Поляков: Тут для лучшего понимания можно сравнить завод с машиной. Вы купили новый автомобиль и три года ездите на нём без проблем. У вас есть гарантийный срок эксплуатации, и вы практически не вкладываетесь в техническую составляющую. Рано или поздно приходит момент, когда гарантия заканчивается и наступает период интенсивной эксплуатации. Каждый раз расходы на техническое содержание будут расти вместе с расходом ресурсов. Если вы проехали на своём автомобиле 250 тыс. километров и не отремонтировали, например, двигатель, то расходуете больше бензина, что экономически нецелесообразно. И здесь есть два варианта: либо заменить автомобиль, что конкретно для нас невозможно, либо отремонтировать имеющийся и вернуть его в базовое состояние. Этим мы сейчас и занимаемся. Возвращение завода в базовое техническое состояние позволяет достичь плановых показателей энергопотребления, основанных на заявленных производителем оборудования технических данных. В результате снижается влияние производства на окружающую среду.
Почему мы не покупаем углекислоту, а сами её воспроизводим с помощью рекуперации?
К. К.: Без углекислоты нормальное и качественное пиво производить нельзя, а она достаточно дорога на рынке. Наша цена — 9 рублей за килограмм, то есть тонна —это 9 тысяч рублей. Мы в месяц потребляем примерно полторы тысячи тонн углекислоты. Если бы мы не занимались рекуперацией, то теряли бы большие деньги. Комплекс проведённых мер — результат командной работы службы эксплуатации, пивопроизводства и цеха розлива.
Что даёт новая система рекуперации заводу?
К. К.: До этого у нас тоже работала система рекуперации, но она не выходила на уровень самодостаточности, то есть нам всё равно приходилось докупать разницу на стороне. Мы подсчитали, что за 2017 год потратили на углекислоту более 30 млн. рублей. Пиво при брожении выделяет избыточную углекислоту, и её достаточно, чтобы вернуть в пиво и сделать его готовым к продаже. А когда ты производишь безалкогольные напитки, то в них изначально нет углекислоты, и ею напиток нужно насытить.
ЧТО ТАКОЕ СИСТЕМА РЕКУПЕРАЦИИ УГЛЕКИСЛОТЫ
Рекуперация углекислоты происходит в несколько этапов:
1. Очистка углекислоты от пены с помощью пеноловушки. Попадание пены в систему рекуперации отрицательно сказывается на работе оборудования.
2. Весь углекислый газ, который вырабатывается при брожении, мы собираем и пропускаем через «водяную баню»: на газ сверху распыляется вода. Это так называемая система скрубберов — аппаратов, промывающих газ с помощью жидкостей. Именно на нашем заводе стоит один скруббер, который обеззараживает углекислоту раствором перманганата калия — это сильнейший окислитель, избавляющий от всех нежелательных запахов.
3. Затем очищенная углекислота собирается в газгольдер — буферную ёмкость, по которой загружается в компрессоры. У нас три компрессора, и в зависимости от загруженности газгольдера включаются либо все, либо только один по определённому алгоритму. Они сжимают газ до жидкого состояния.
4. Далее газ пропускается через угольный фильтр, то есть через активированный уголь, где оседают оставшиеся запахи.
5. Жидкая углекислота проходит отделение неконденсируемых газов и теряет не сжатый газ. Это, как правило, воздух, потому что у него давление конденсации намного выше. Наша задача — полная очистка CO 2.
То есть сейчас нам хватает CO2 и на производство пива, и на безалкогольные напитки. При этом даже остаётся лишнее.
А. П.: На работу системы очень влияет планирование, то есть соотношение сваренного пива к разлитому всегда должно быть примерно одинаковое. Если мы, например, разливаем больше, а варим меньше, то у нас будет просадка по получению углекислоты.
Что происходит с чистой углекислотой?
К. К.: Мы храним её в двух танках по 100 тонн каждый. Оттуда углекислота идёт на производство, запускается обратный процесс перевода жидкой кислоты в газообразное состояние. У нас пиво нигде не соприкасается с воздухом, ведь для него это главный враг. Всё делается через CO 2.
Говорят, что на углекислоте можно заработать. У нас получилось?
К. К.: Да, получилось. В апреле мы сами впервые продали 20 тонн углекислоты.
Кто стал покупателем?
К. К.: Та же фирма, у которой раньше мы покупали CO2. Мы продали по заниженной цене, потому что в этой сделке они полностью занимались логистикой. Их фирма может хранить эту углекислоту долгое время. Если вдруг она снова нам понадобится, они смогут её привезти.
Знаю, что во время чемпионата мира по футболу в России мы чуть не остались без углекислоты. Расскажете?
К. К.: В связи с ужесточением мер во время мундиаля в прошлом году закрывали некоторые химические заводы с опасными производствами. Наши поставщики CO 2 тогда сказали, что они физически не смогут снабжать завод углекислотой. Если бы мы к началу «ЧМ» этот вопрос не решили, то из-за нехватки CO 2 могли реально остановить завод.
То есть нам в какой-то степени повезло?
А. П.: Да, со своевременной оптимизацией системы рекуперации мы прямо угадали.
Какая перспектива у этого направления?
К. К.: В мае мы получили декларацию о соответствии нашей углекислоты всем необходимым стандартам и теперь являемся полноценным продавцом CO2.
В апреле 2019 года система рекуперации углекислоты Московской Пивоваренной Компании впервые обеспечила положительный прирост её запасов. Это стало возможным благодаря повышению эффективности сбора CO2 и сокращению потерь на производстве. До этого заводу приходилось докупать углекислоту по рыночной стоимости, на порядок превышающей себестоимость собственной выработки.
Зачем нужна биологическая очистка стоков?
К. К.: Мы сбрасываем сточные воды в реку Яузу. Это самый жёсткий сброс с точки зрения требований к качеству сточных вод, потому что в реках есть рыба, и наше производство не имеет права ухудшать экологическую ситуацию.
А. П.: Если мы сбросим неочищенный сток, это может повлечь за собой усиленный рост водорослей, которые интенсивно потребляют кислород. При отсутствии кислорода в воде вся рыба погибает.
Как с помощью стоков вырабатывать электроэнергию?
К. К.: Стоки — это раствор питательной среды для бактерий, живущих на очистных сооружениях. Бактерии, поедая питательные вещества, вырабатывают газ метан. Он направляется в газопоршневые установки, которые сжигают его и вырабатывают электроэнергию.
Какие объёмы эта система пропускает через себя?
К. К.: Она вырабатывает порядка 10% от нашей потребляемой электроэнергии, и очистные сооружения могут автономно работать только благодаря этой системе. То есть это тоже элемент энергоэффективности.
А. П.: На общее производство этого не хватает, вся вторичная электроэнергия используется только для работы очистных стоков. Именно здесь мы экономим.
Зачем нужно рекуперировать энергию пара при кипячении сусла?
К. К.: Опять же для экономии. Это вторичное использование энергии. Существует аккумулятор — ёмкость с большим объёмом воды. Эта вода набирает тепло и затем разогревает сусло. Тепло получается за счёт того самого вторичного пара, который образуется при кипячении сусла. Затем эта вода идёт на разогрев следующей партии сусла. Изначально сусло имеет температуру 78 градусов. Вода из аккумулятора нагревает его до 95 градусов, и затем мы паром поднимаем температуру ещё на 5 градусов, чтобы оно вскипело. Если бы мы не использовали вторичный пар, то нам приходилось бы разогревать паром сусло с 78 градусов до 100. Именно таким образом завод экономит природный газ и пар, а мы снижаем нагрузку на работу котлов, которые этот пар производят.
Какие планы на будущее? Можно ли сказать, что сейчас все процессы на заводе самоокупаются?
К. К.: Пока мы только в начале пути. Какие-то результаты уже достигнуты, но это ещё не конец. Как я и говорил ранее, у нас есть цели по снижению удельного потребления энергоресурсов.
А. П.: Например, у нас пока нет нужды самим вырабатывать воду. Налог на добычу водных ресурсов в нашей стране отличается от европейского. У нас добыча одного литра воды стоит 50 копеек, что крайне низко. Поэтому сейчас мы пока об этом не беспокоимся. Как только государство поднимет водный налог, будем думать над новыми проектами в этой области. Также хочется добавить, что, на мой взгляд, сейчас самое главное — это работа с людьми. Это основополагающее звено в любом процессе. Мы планируем повышать культуру энергосбережения. Эта программа призвана донести до сотрудников концепцию ответственного потребления и применения энергетических ресурсов, ведь они не бесконечны.
We use cookies and other similar technologies to improve website work